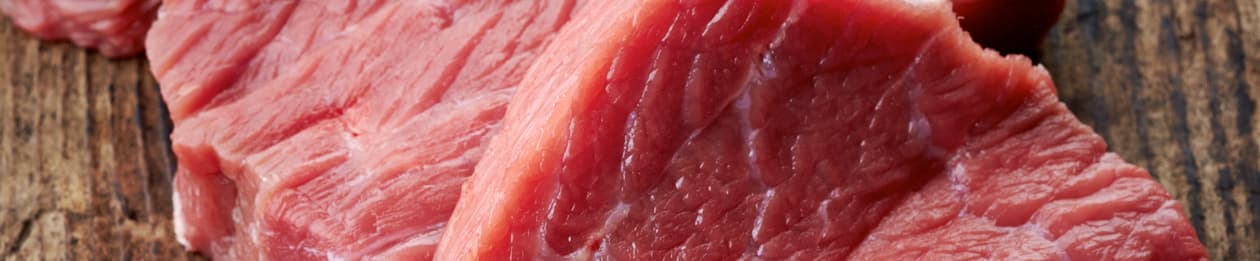
In 1953, Birko was founded to address challenges facing the protein and protein harvest industries. For over 60 years we’ve been a preferred partner for beef, poultry and pork processors based on a comprehensive understanding of the needs and challenges facing you.
Whether you are looking to improve your sanitation procedures, address a Listeria outbreak, or install a custom equipment and chemical solution, our team of experienced and highly trained employees are here to help you.
Contact Birko for:
Experienced microbiologists, chemists, technical sales representatives, engineers, and quality assurance professionals are available to work directly with you for the custom solution your facility requires. HACCP, SQF, and BRC certified professionals; you name it, we have them on our team.
Our team of industry trained professionals conduct the most robust sanitation and process assessment available.
We not only identify best practices, but we’ll also train your team to implement and maintain documented, repeatable practices that help ensure a safe product.
Interested in equipment custom crafted for your facility with sanitary design in mind? Designing and building innovative products for over 40 years, Birko’s equipment experts can help you build or upgrade your facility with efficiency, safety, and sanitary design in mind.
Need a tailored solution for your unique facility? We can help. Birko’s technical experts build specialty chemical formulations, including custom chemical blending and CIP plant cleaning chemicals.
We are your partner in food safety. In fact, our people and services are why companies choose us and remain loyal customers. Hear what some of our protein customers are saying about us.